Dan Hahn, Vice President of ATS Lean Scheduling International, with over 20 years in manufacturing technologies including system selection, project management, implementation, and development.
Whether you have a Just-in-Time (JIT) program in place with your vendors or if your customers have a JIT program in place with you, it becomes obvious that one side is getting the benefit and the other is taking the risk. We all understand the benefits of Just-in-Time:
- Reduced inventory/warehousing
- Efficiencies in the flow of product
- Better handling of changeovers
But whether you are on the supplying or receiving end, there are always risks involved with the potential disruptions in the supply chain. Suppliers to JIT customers often mitigate those risks by keeping distribution centers stocked with products, but this reduces efficiency for the supplier and adds cost. Let’s break this down.
Supplying Just-in-Time
As a manufacturer supplying Just-in-Time customers, it is your responsibility to keep products flowing regardless of how it impacts your efficiency, cost, inventory levels, or on-time delivery to other customers. Most JIT suppliers will receive a forecast from their customer and will build to forecast with a safety stock to allow for potential supply chain issues.
The only way to offer JIT while keeping cost down and efficiencies up is to have full visibility to your customer’s demand, your production capacity, as well as your inventory levels and your supplier’s ability to deliver. This is a lot to ask of your ERP/MRP system. Even though ERP stands for Enterprise Resource Planning, it really does everything but planning. The missing link is Advanced Planning and Scheduling (APS) along with a comprehensive forecast that incorporates your customer’s forecast. These systems provide the visibility not only to your production, but also to your inventory and purchase orders as they relate to your production. Let’s take a look at each element:
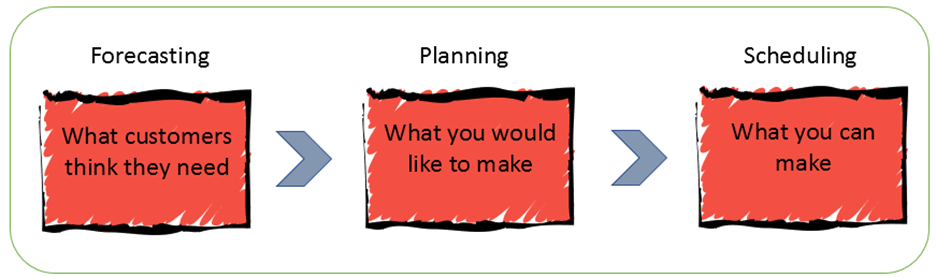
Forecasting
You will often hear that the forecast is never right. That is true, but it doesn’t have to be 100% accurate. It just has to be as close as you can get it. With enough historical data, a statistical forecasting tool will analyze several years of demand and determine the best statistical method of forecasting. The key is the ability to collaborate using the output of the statistical forecast with customers and salespeople to adjust for any outside factors that may affect demand. Having both a short-term forecast and a longer-term forecast is what will drive your production decisions along with your purchasing decisions.
Planning
The plan is where you will look to balance:
- What you would like to make— Your total forecast and demand (sales orders)
- What you have capacity to make
- Where you want to make it— Level loading between plants or production lines
To produce “What you need to make…”
In an over capacity situation, the planning tool is critical in determining where to balance forecast against demand so that you are satisfying customer demand without adversely affecting future demand. This allows you to smooth your production runs as you hand off your plan to the scheduling tool, reducing short inefficient runs.
Planning is also where you will have visibility to inventory requirements to handle long-term buys, volume purchases, as well as the ability to provide visibility to your suppliers. Material Requirements Planning (MRP) is supposed to handle short- and long-term purchases, but it fails in one respect. It has no visibility to actual production. MRP ends up telling you to order raw materials when it would like you to produce finished goods, not when you actually have the capacity to produce the finished goods.
Scheduling
The schedule is where we determine:
- How best to make it— Which machines & other resources to schedule
- How to sequence the production to:
- Increase efficiency
- Balance on-time delivery
- Reduce changeover times
- Reduce downtime by scheduling only work orders with available raw materials
A quality Advanced Planning & Scheduling solution will provide visibility to forecast, sales orders, raw material inventory, sub-component inventory and work orders, finished goods inventory, and purchase orders. The scheduling system utilizes all of this information to schedule orders that:
- Have available raw materials
- Have available sub-component materials or consider work orders that create those sub-components
- Have enough capacity on the equipment that is required
- Have sufficient operators, tooling, etc. to run the equipment
Once this criterion is met, the scheduling system will focus on the best sequence on each line or resource it is scheduling on, based on different sets of rules such as:
- Forward scheduling by due date— This rule will strictly line up orders based on their due date priority. The advantage of this rule is that it focusses on on-time delivery but at the expense of efficiency in reducing changeover time.
- Minimize setup time— This rule will look at different attribute matrices and compare the operation that is currently scheduled on the line to determine the least amount of setup time of all of the operations that are in its queue. For example, if I have the choice of taking a half an hour to go from red to white and from a 30″ width to a 40″ width -or- 5 minutes to go from red to red, and a 30″ width to a 32″ width, it will select the latter.
- Preferred sequence— This rule is similar to minimize setup with the exception that it does not require a matrix to determine each incremental setup time change. You can simply say that the first criteria is color and the second criteria is width. The advantage to this is that it is easier to setup and maintain but doesn’t give the precision of minimize setup.
These are just a few examples in a world of possibilities. Having the visibility of your production as well as your supply chain is critical to removing the guess work required to provide Just-in-Time, while keeping inventories to an acceptable level. Having the proper tools to provide this visibility and the ability to react to change as it happens is the key to keeping up with your JIT customers. That’s exactly what Advanced Planning & Scheduling does for you and why it is absolutely necessary for Just-in-Time manufacturers.
Pingback: What are the 5 Steps to Production Planning? - Lean Scheduling