In the competitive and complex world of manufacturing, capacity planning software plays an important role in streamlining production processes, optimizing resource allocation, and ensuring timely delivery of products. However, the path to achieving these benefits is fraught with potential pitfalls. This blog post highlights critical mistakes to avoid when deploying and utilizing capacity planning software in a manufacturing context, ensuring your operations are as efficient and productive as possible.
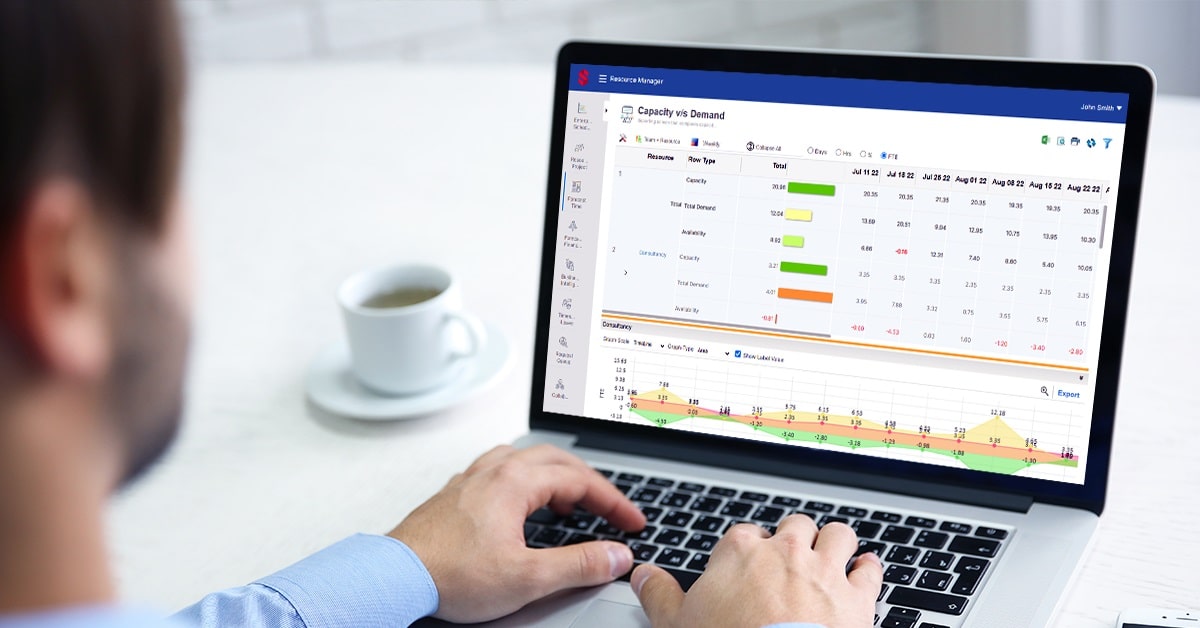
Overlooking Manufacturing-Specific Requirements
A common error is failing to consider the unique demands of the manufacturing sector when selecting capacity planning software. Manufacturing operations require software that can handle intricate production schedules, manage machine and labor capacities, and adapt to sudden changes in demand or production line issues.
Key Takeaway: Choose capacity planning software tailored to the complexities of manufacturing, with features designed to manage the specific challenges of production environments.
Neglecting Real-Time Data Integration
In manufacturing, conditions on the shop floor can change rapidly. Relying on outdated or static data can lead to inefficiencies and bottlenecks. It’s vital that the capacity planning software integrates seamlessly with real-time data sources, such as IoT devices and ERP systems, to accurately reflect current production capacities and constraints.
Key Takeaway: Ensure your software can integrate with real-time data sources for up-to-date planning and decision-making.
Underestimating the Importance of Scalability
Manufacturing demands can fluctuate due to seasonal trends, new product launches, or shifts in consumer demand. A mistake often made is choosing capacity planning software that cannot scale up or down easily with these fluctuations. This lack of scalability can hinder your ability to respond to market changes efficiently.
Key Takeaway: Opt for scalable capacity planning software that can adjust to varying levels of production demand.
Ignoring User Training and Engagement
The sophistication of advanced planning software necessitates thorough training and user engagement. Without it, even the most powerful tools can become underutilized or misused. A well-trained workforce can leverage the software to its full potential, identifying opportunities for efficiency improvements and proactive problem-solving.
Key Takeaway: Invest in ongoing training and encourage user feedback to maximiser the benefits of your software.
Failing to Align with Business Objectives
Capacity planning software should be a means to achieve broader business goals, such as reducing waste, improving product quality, or increasing customer satisfaction. Not aligning the software’s use with these objectives can lead to misdirected efforts and missed opportunities for improvement.
Key Takeaway: Regularly review how the capacity planning software aligns with and supports your manufacturing objectives.
Overcomplicating the Implementation
Introducing complexity into the planning and implementation phases can delay or derail the deployment of capacity planning software. Simple, phased approaches allow for better understanding, easier troubleshooting, and more effective training, ensuring a smoother integration into existing processes.
Key Takeaway: Adopt a streamlined approach to implementing capacity planning software, focusing on core functionalities before expanding features.
Dismissing Continuous Improvement and Adaptation
The manufacturing landscape is constantly evolving, with new technologies, materials, and methodologies emerging. Treating capacity planning software as a set-it-and-forget-it tool can prevent your manufacturing operations from adapting to these changes and improving over time.
Key Takeaway: Promote a culture of continuous improvement, using insights from your capacity planning software to refine and adapt your manufacturing processes regularly.
Capacity Planning Software FAQs:
Q: How does Capacity Planning Software improve decision-making?
A: By providing real-time data and predictive insights, it enables managers to make informed decisions quickly, adjusting plans to meet changing demands.
Q: Can small businesses benefit from Capacity Planning Software?
A: Absolutely. Small businesses, in particular, can gain a competitive edge by optimizing their resources and responding agilely to market demands.
Q: Is Capacity Planning Software difficult to integrate with existing systems?
A: While challenges may arise, many modern solutions are designed for easy integration with existing business systems, minimizing disruption and enhancing data synergy.
Conclusion
Avoiding these mistakes can significantly increase the effectiveness of capacity planning software in a manufacturing context, leading to improved production efficiency, better resource utilization, and higher product quality. By carefully selecting & partnering with the right team of APS experts, implementing the right software, and committing to ongoing improvement, manufacturers can achieve a competitive edge in the dynamic and demanding manufacturing industry.
Pingback: Top Mistakes to Avoid When Using Capacity Plann...
Pingback: Common Mistakes to Avoid When Using Capacity Planning Software – Lean Scheduling International