Article by ATS Project Engineer, Joao Thiesen
Production planning and scheduling processes are long-time friends for those working in a factory or similar business, dealing with supply chain fluctuations, deadlines, and other challenges to deliver a product or service to meet customer demand.
In most manufacturing environments, tasks like reprioritizing product or sales orders, collaborating with other teams to address material shortages, or reacting to machine downtime, are likely part of daily operations, albeit possibly on different scales. This is all related to production planning and scheduling. However, planning and scheduling processes are very different from one another.
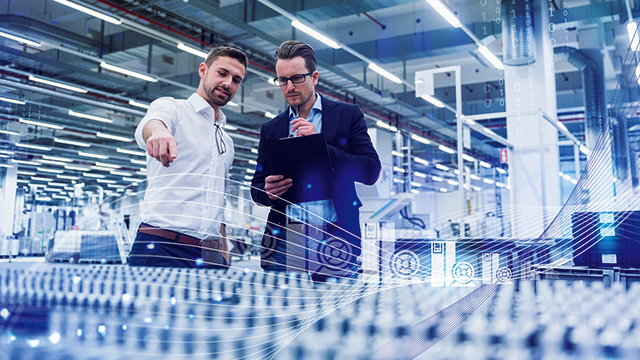
What distinguishes planning from scheduling in manufacturing?
So, what is the difference in planning & scheduling? The key differences lie in the time horizon and level of detail. These processes can be handled separately by different teams or combined into a single process flow.
Let’s outline some tasks associated with each process:
Planning:
1. Demand Analysis: Consider short to long-term sales orders, supplementing the information with reliable forecast data.
2. Capacity Analysis: Understand nominal capacity, considering bottleneck resources or the most restrictive ones. Account for shifts, large maintenances, and potential constraints like resource groups.
3. Product Mix: List all active and potential new products, understanding the processing capacity each batch or unit requires.
4. Supply: Utilize traditional Material Requirements Planning (MRP) methods to calculate material and Work in Process (WIP) needs, relying on stock levels, shelf-life, expiration dates, and trustworthy suppliers.
Scheduling:
1. Workcenters and Secondary Constraints: Assess real capacity with detailed information on calendars, shifts, available labor, molds, auxiliary equipment, and cleaning rules.
2. Materials and Supply: Validate standard Bills of Materials (BoM), check stock levels, confirm promised delivery dates from purchase orders, and ensure material quantities align with work orders.
3. Factory Rules: Validate rules allocating products and materials to workcenter resources, considering sequences, previous and/or next operations to avoid issues on the shop floor.
4. Demand: Continuously check sales order priorities, stock levels, and anticipate any potential demand changes.
What types of decisions are made in planning vs scheduling?
Both planning and scheduling involve critical decision-making to address current factory status and create ‘What-if’ scenarios for mid- and long-term management planning. Depending on the shop floor rules & business model, the list of decisions can be extensive, but let’s consider the most common questions to be answered for optimal decision-making in both planning & scheduling:
Planning:
- What is my available capacity for the next few months?
- Do we need to acquire more workcenters?
- If we add additional workcenters, how much demand fulfillment can I increase?If we stop/sell some workcenters or reduce my shifts or working days, what is the impact?
- If some workcenters are heavily loaded, can we change our product mix or adapt the workcenters to run other products to rebalance capacity?
- What is the risk on demand if a lower my safety stocks?
- If my forecast changes to higher levels, will we be able to deliver every sales order?
- If the forecast gets lower, can I reduce some shifts or labor and still deliver the amount needed of my products?
- If we know what materials we need and their quantities for the next few months, do we need more suppliers?
- Will our current partners be able to deliver on required dates and volumes?
- What is the impact if a supplier stops selling to us?
- Can we make a new deal if we increase our volume?
Scheduling:
- What is the best schedule that I can create with the current work orders and workcenters?
- If I optimize the product sequence on the workcenters to minimize setup, will my sales orders be fulfilled on time?
- What if I change some products to run on an alternative machine, will the capacity be better balanced?
- Some orders are scheduled late because of material availability…
- Can we change the BoM to use alternative material?
- We are missing some materials from stock, should we contact the supplier to anticipate the deliveries?If we split batches and run in parallel workcenters, is this a better decision?With the current schedule, which resources will need longer cleaning?
- Which materials are needed for today and in which order and times?
- What is the impact if we change shift durations?
- If we reduce the working week, will this cause certain sales orders to be late?
- Are we able to schedule planned maintenance within the next days?
- We are falling behind in production; how many additional hours are needed to get caught up?
- We are short on specific labor… if we increase, will this allow more throughput?
- If we purchase additional auxiliar machines or molds, can we increase the sales of a certain mix of products?
- We are considering shutting down the 2nd shift for a week, what orders will be late?
- Which demands are priority and need a safety net of stock?
- Which sales orders are at risk of being late?
- A client asked to change the due date for some items, can we achieve that?
Should your company focus on planning, scheduling, or both?
There is no simple answer to this question and a deeper discussion about the business processes is necessary, but in most cases, yes, both are needed. Planning and scheduling are complementary processes that can be done by different teams, involving more than one specialist, with many points of view, discussions, and constantly changing decisions.
If a company has solid MRP (Material Requirement Planning) and MPS (Master Production Schedule) data for the upcoming weeks/months, perhaps simple planning would suffice. The planner could communicate the information, allowing the shop floor leaders to deal with the product mix, and material could then be purchased on time and in the correct quantity.
However, the company will need to implement a planning process if there are problems related to a lack of vision into future production. If you can’t see which demand needs to be met and what materials are required over the coming weeks, it’s likely that your shop floor is working on the orders with higher demand. Throughout the day, chaos ensues with constant change and teams running to get materials to the shopfloor to simply survive.
On the other hand, even if the planning process generates a good result but the product mix and complexity of production requires too many possible combination scenarios and rules, a scheduling process would be required. Efficient scheduling helps validate complex production rules, check materials and demand, generate schedules considering constraints (labor, tooling, materials, maintenance, run times, cleaning, etc.), and streamline operations.
In conclusion, deciding whether to implement planning or scheduling processes/solutions depends on your company’s needs. One thing is for certain, having both provides comprehensive insights and will most likely boost overall productivity, efficiency, and profitability.
Pingback: Trade-offs between Production Planning & Sh...