Production planning is a strategic process used by businesses to efficiently organize and coordinate all the resources and activities involved in manufacturing goods or providing services. It aims to ensure that products are produced in the right quantity, at the right time, and at the right cost to meet customer demands while optimizing the utilization of resources. The production planning process typically involves several key steps to ensure the efficient and effective manufacturing of goods.
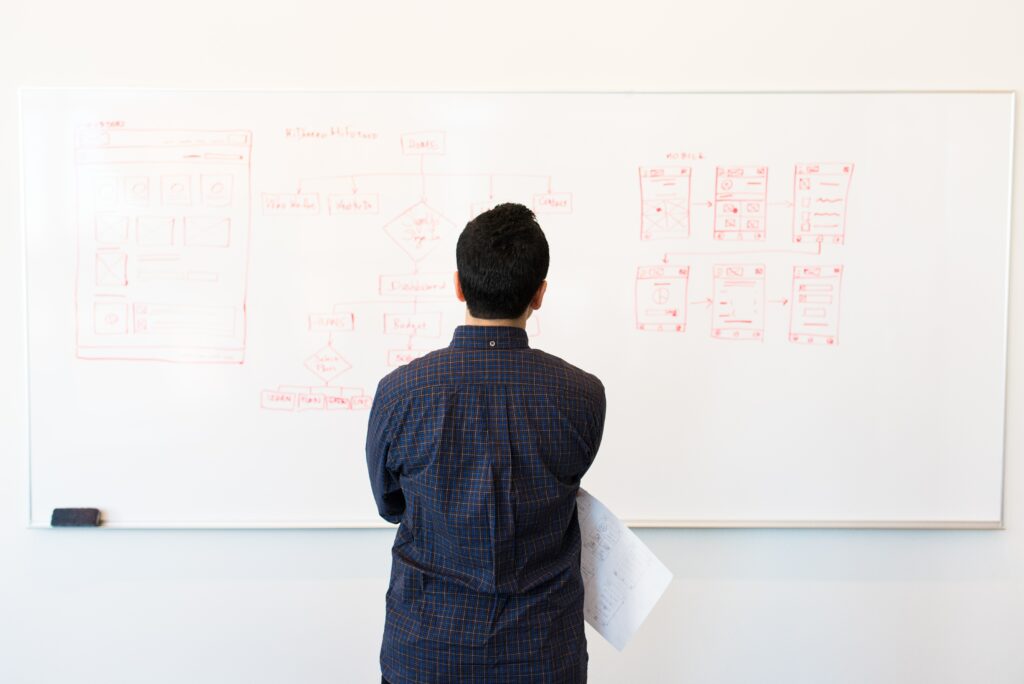
While there can be variations based on the industry and specific needs of a company, here are the five common steps in production planning:
1. Demand Forecasting: Demand forecasting is the foundation of the production planning process. By analyzing historical sales data, market trends, customer preferences, and other relevant factors, companies can estimate the future demand for their products. This step helps them avoid underproduction or overproduction, both of which can be costly.
Accurate demand forecasting enables companies to align production with customer requirements, preventing stockouts and ensuring that customers receive their orders on time. Moreover, it allows businesses to plan for potential demand fluctuations and seasonal variations, helping them stay ahead in the market.
2. Resource Assessment: Once the expected demand is forecasted, the next step is to assess the resources required for production. This assessment involves evaluating the availability of raw materials, equipment, labor, and production capacity.
Resource assessment is crucial in identifying potential bottlenecks and constraints that could hinder the production process. For example, a shortage of raw materials or a lack of skilled labor might slow down production and affect delivery timelines. By identifying these limitations early on, companies can take proactive measures to address them and ensure smooth operations.
3. Production Scheduling: Production scheduling involves creating a detailed timetable that outlines not only when and how much of each product should be manufactured but also “how best” to run production. The schedule considers various factors such as production lead times, setup times, machine availability, and resource constraints.
An optimized production schedule helps streamline the manufacturing process, maximizing resource utilization and reducing idle time. This, in turn, leads to increased efficiency and minimized production costs. The schedule also facilitates coordination among different departments and stakeholders involved in the production process.
4. Inventory Management: Effective inventory management is a critical aspect of production planning. Striking the right balance between having enough stock to meet demand and avoiding excess inventory is essential.
Just-in-time (JIT) inventory practices and safety stock measures are commonly used to maintain optimal inventory levels. JIT involves receiving raw materials and producing goods only as they are needed, minimizing inventory holding costs. Safety stock acts as a buffer to handle unforeseen changes in demand or supply chain disruptions, ensuring continuity of production even during uncertain times.
5. Monitoring and Adjustments: Production planning is an ongoing process that requires continuous monitoring and adjustments. Companies need to compare actual production against the planned schedule to identify any deviations or discrepancies.
Unforeseen changes in customer demand, supply chain disruptions, or production issues may necessitate adjustments to the production plan. By promptly responding to these changes, companies can mitigate risks, avoid delays, and maintain customer satisfaction.
Incorporating advanced technologies and data analytics for production planning
To manage the production planning process more effectively, it’s crucial that manufacturers today integrate advanced technologies and data analytics in their production planning process. These technologies can enhance the accuracy and efficiency of production planning by providing real-time data insights, enabling better decision-making.
For instance, predictive analytics can help improve demand forecasting by analyzing historical data and identifying patterns and trends. The use of machine learning algorithms can optimize production schedules based on various factors, such as resource availability, production capacity, and market demand. Additionally, IoT devices and sensors can enable real-time monitoring of production processes, allowing companies to detect and address issues promptly.
So, now what?
Seamless and efficient manufacturing of goods hinges on an effective production planning process. By methodically strategizing around each of the five steps outlined in this post and harnessing the power of advanced technologies and data analytics, manufacturers can gain a competitive edge over their rivals. The path to success becomes clear when companies master the art of the production planning process, enabling them to meet customer demands with precision and optimize resource utilization.
If you’re unsure how to take the next step in improving or enhancing your production planning process, our skilled team of consultants is ready to come alongside you. No two manufacturers are exactly alike, so to use a “cookie cutter” approach would be unsuccessful and could even be damaging to the business’s productivity & outcome. However, our consultants’ understanding & expertise allows for the effective implementation of the production planning processes & solutions that will revolutionize your unique business and your bottom line.
Pingback: What are the 5 Steps to Production Planning?&nb...