LSI Case Study
Opcenter (Preactor) APS
Koch Foods - Opcenter Planning & Scheduling Case Study
Creating a planning and scheduling solution to address limitations and improve operational efficiency
Adapting to customers' needs
Koch Foods is a leading poultry processor in the U.S., known for its commitment to producing high-quality products and providing service throughout poultry growing, manufacturing and distribution processes. Over the past 30 years, Koch Foods has grown from a small operation to one of the largest vertically integrated poultry processors in the country. The company focuses on delivering smaller, high-quality meat products and adapting quickly to changing customer needs and market trends.
Over those 30 years, Koch Foods encountered several challenges in its operations. Specifically at its production plant in Fairfield, Ohio, the company lacked a proper planning mechanism to anticipate the impact of increased demand on its production capabilities. It would run into continual changes based on demand dates such as orders constantly changing because of normal production influence, products not showing up on time, changes to customer orders, products that do not fit the production plan due to wrong trim and incorrectly sized meats, amongst other issues. The team would have to shut lines down, clean them and start back up because they were missing orders.
Relying on tribal knowledge
Without a clear understanding of cause and effect, the company would make ad-hoc adjustments to workorders, often leading to inefficiencies and a constant state of “fire drill” mode for planners and schedulers. The absence of a production planning method made it difficult to account for growth, resulting in a heavy reliance on tribal knowledge and gut instincts.
Additionally, scheduling around allergens and managing ingredient variations posed further difficulties and often lead to costly setups, cleanouts, and changeovers. To combat these issues, Koch Foods worked with ATS Lean Scheduling (LSI), a trusted Siemens Digital Industries Software partner, to use Opcenter™ APS software to streamline operations. Opcenter is part of the Siemens Xcelerator business platform of software, hardware, and services.
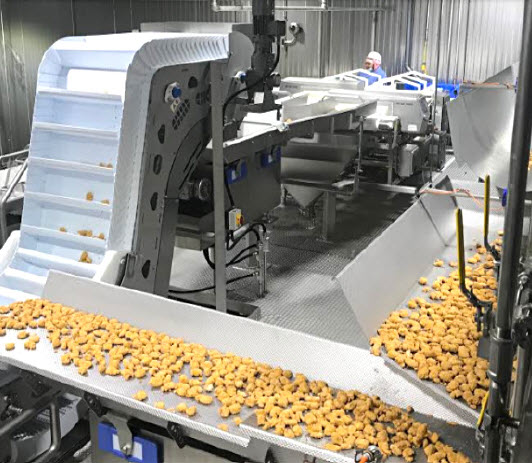
Using Opcenter APS helped Koch reduce costly changeovers, enhance training for planners and schedulers and minimize reliance on tribal knowledge.
Streamlining production planning & scheduling
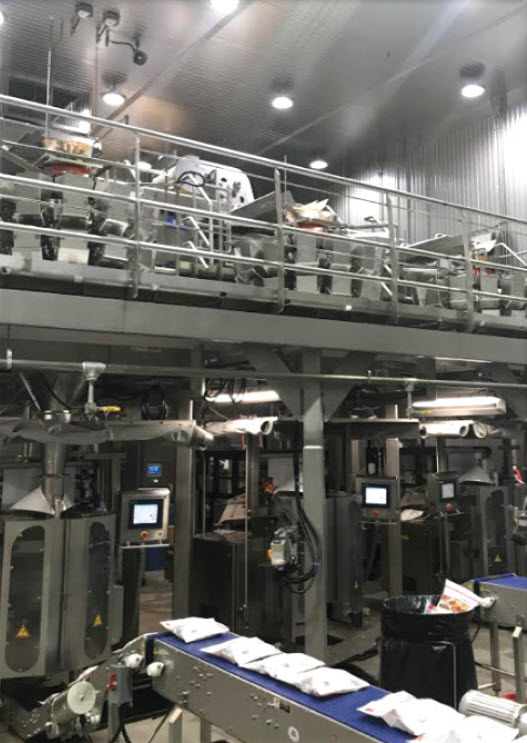
Koch Foods aimed to maintain growth and improve operational efficiency without significantly increasing its number of employees. To address these challenges, Stewart Ward, vice president (VP) of information systems at Koch Foods, first looked into material requirements planning (MRP) systems, but quickly noticed that most MRP systems would displace (take over the role) of functionality in their existing enterprise resource management (ERP) system, which they did not want to do. Ward then looked into planning and scheduling solutions but most he found were modules tied to an ERP system. He then looked specifically for standalone APS solutions when he came across Opcenter APS through a trusted recommendation.
Koch Foods partnered with LSI to implement Opcenter APS in several ways. LSI conducted an on-site assessment to understand Koch Foods’ challenges, goals, and requirements. This assessment allowed LSI to thoroughly analyze Koch’s data and processes. LSI also built customized reports that assisted during the implementation, including an MRP report that uses the schedule and pegging to show shortages. This MRP created visibility into what the company needed to buy to meet its short-term goals.
Following the assessment, LSI carried out a proof of concept using a sample of Koch’s own data, which confirmed that Opcenter APS was the right solution for the company. “When Brian Reisen, the general manager at the Fairfield plant, looked at the Opcenter APS planning interface that had been put up on the screen, he said, ‘that’s exactly what we’re looking for… that’s what we want to be able to get to,’”, says Ward.
LSI’s collaborative approach, deep understanding of Koch’s needs and ability to translate requirements into the solution played a crucial role in building consensus and confidence among the stakeholders.
Koch Foods was able to cut back on operations and overtime hours, transitioning from a 7-day workweek to a controlled 5-day or 6-day schedule.
Optimizing production plans
Using Opcenter APS provided Koch Foods with a planning and scheduling solution that addressed its limitations and improved operational efficiency. The Opcenter APS modeling capabilities allowed Koch Foods to optimize production plans to consider allergens, setup requirements, shift patterns, machine capacity and material availability.
By integrating Opcenter APS with Koch’s ERP data and demand forecasts, the Koch Foods team gained visibility into the entire production process, which enabled more efficient order sequencing. Using Opcenter APS helped them reduce costly changeovers, enhance training for planners and schedulers and minimize reliance on tribal knowledge. The solution’s scalability and ease of modification ensured ongoing support and adaptability across the entire production process.
Implementing Opcenter APS brought significant benefits to Koch Foods. By maximizing production throughput without adding costly resources, the company achieved notable financial gains. Koch Foods was able to cut back on operations and overtime hours, transitioning from a 7-day workweek to a controlled 5-day or 6-day schedule. Now, this five- or six-day schedule is a much more controlled schedule with fewer packaging problems and more predictability.
Koch Foods optimized its existing plant resources, running at 95 to 100 percent capacity every day. The improved planning and scheduling processes led to increased productivity, streamlined operations and better resource utilization.
By implementing Opcenter APS and working with LSI, Koch Foods revolutionized its planning and scheduling processes and will continue to use Opcenter APS in continuing to streamline production operations.
Scheduling with Allergens – Opcenter APS
Intro to Opcenter APS Features
Webinar: APS for F&B Industry