Opcenter (Preactor) Advanced Planning & Scheduling
Siemens Opcenter Advanced Planning & Scheduling (formerly Preactor) has the largest installed base of any independent production planning and scheduling software in the world. With over 10,000 licenses shipped, more than 6,500 companies use Opcenter (Preactor) Advanced Planning & Scheduling worldwide. LSI has implemented the Opcenter APS solution since 2001, with over 80% of the North American Opcenter APS users in our client base.
A visual, heuristics-based production planning & scheduling solution for manufacturers...
Opcenter Advanced Planning & Scheduling (APS) is not a single point solution. It is a family of products that have different levels of functionality and pricing so you can select the system that satisfies both your needs and budget. Opcenter APS can be used for long-term strategic planning (Opcenter Planning) covering months and years ahead, medium-term tactical planning with a few weeks planning horizon, and for detailed sequencing and scheduling (Opcenter Scheduling).
Nearly 350 manufacturers in North America, covering almost every manufacturing sector and ERP system, use Opcenter. ATS Lean Scheduling International has been implementing Siemens Opcenter (formerly Preactor) Advanced Planning & Scheduling software solution since 2001, and has the largest installed base of any Opcenter Planning & Scheduling partner in North America. Over 80% of all Opcenter APS installs are within the LSI client base.
Although Siemens Opcenter Advanced Planning & Scheduling software solution provides great functionality out of the box, its real power is that it is a complete tool set for building production scheduling solutions. Like a Lego set, it can be used to build your own unique manufacturing production scheduling solution which is what sets it apart from other APS solutions.
If you are satisfied with a mediocre manufacturing production scheduling solution, then there is no need to choose Opcenter APS, but if your intent is to create a scheduling solution that delivers immediate results while laying the groundwork for unlimited future improvements and innovation, then you need Siemens Opcenter Advanced Planning & Scheduling.
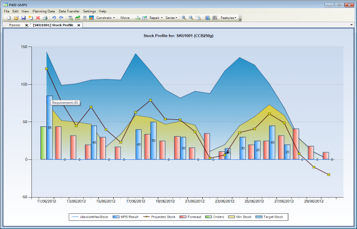
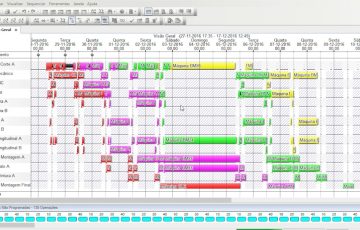
It is not always easy for others to understand what makes Siemens Opcenter Advanced Planning & Scheduling software solution work when other systems don’t, but its approach is fundamentally different. Most of the systems being offered today are based on algorithmic sequencing (optimization) techniques. Although Siemens Opcenter Advanced Planning & Scheduling software solution can use algorithmic sequencing, it is primarily based on heuristics (rules) and it does not claim to “optimize” your master production schedule. Optimizing sounds wonderful, but in most cases, it is totally unrealistic and leads to disaster. The difference may sound insignificant, but having the ability to build your tribal knowledge into your manufacturing production scheduling solution is what allows you to take what has worked for you and just automate it. In a nutshell, this is what makes it work in the real world.
Another dose of reality is that in our 20+ years of experience we have seen that it is almost impossible to identify all your scheduling requirements before you start your APS project. APS solutions built on algorithmic sequencing can be severely limiting and may not be able to replicate your needs. This means that even if your changes are possible (and they often aren’t), the developer is the only one who can make them. You are then at the mercy of the developer. Since Siemens Opcenter Advanced Planning & Scheduling is built with heuristics (rules), there is no need to involve the developer as you have complete control of the way the system behaves.
Signs that Your company needs an APS solution
High WIP & Stocks
Low Productivity
Delays & Breaks
Missed Delivery Dates
About Opcenter APS...
Faster
Schedules in minutes
Heuristic approach
Frequent reschedule
Deviation management
Quick problem detection
Smarter
Graphical tool
Cause & effect analysis
Frequent reschedule
Identify problems
Fix issues before they happen
Effective
Improved customer service rate
Productivity increases
Inventory reduction
Cycle time reduction
Fast return on investment
Flexible
Configurable workspace
Flexible data structure
Full API (programming interface)
Integrated reporting tool
Unattended scheduling
Flexible sequencing by constraints
Scalable
Integrates to your current systems
Solution evolves with your company
Part of a family of products
From Small/Mid-Size to Fortune 500
Adopted Worldwide
Technically superior
Multi-language
Seamless integration
Global support
Largest install base of any APS
Easily Integrated
No matter your ERP, Opcenter APS easily integrates with its built-in API...
Opcenter APS realized benefits...
Opcenter APS In Action...
Opcenter Scheduling Preferred Sequencing
Opcenter APS Drag & Drop Functionality
Opcenter Planning Parameters
Planning vs. Scheduling
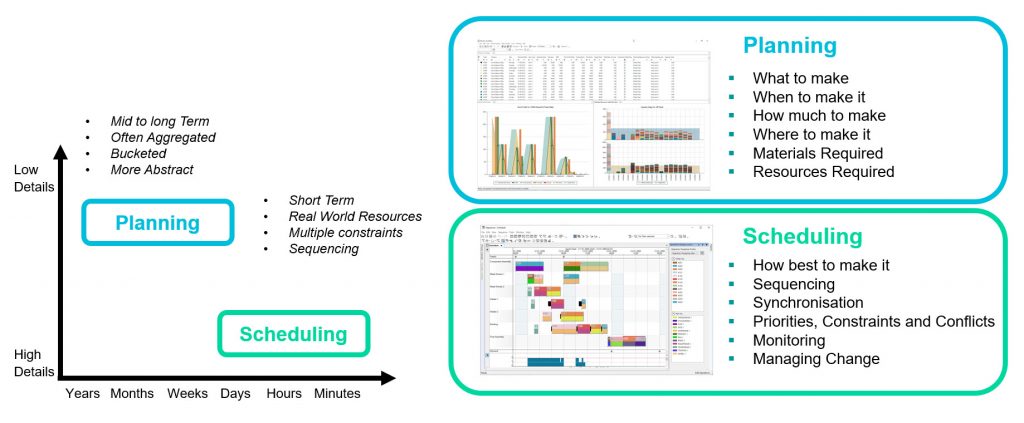