Opcenter (Preactor) Planning
Siemens Opcenter Advanced Planning (formerly Preactor) software is a strategic decision production planning software tool designed to aid you in long- and mid-term planning. It considers forecast and long-term orders, supports decision making about feasibility, & effects the general direction of production.
Siemens Opcenter (Preactor) Advanced Planning software supports major production capacity decisions surrounding extending the work force, resource capacity, and factories. The solution boosts your production planning by better helping you you determine what and how much to make, where and when to make it, and exactly what materials and resources are required.
Siemens Opcenter (Preactor) Advanced Planning can be executed in finite or infinite capacity mode, and planning time periods can be days, weeks, months, or a combination of all three. If used together with Siemens Opcenter (Preactor) Advanced Scheduling solution, detailed production schedule information can be sent back to the planning system to override planned volume with scheduled volume. Master production schedule (MPS) can then be recalculated using production schedule as the base for new results.
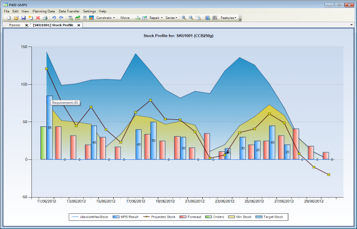
Visualization of the capacity planning chart within Opcenter (Preactor) Advanced Planning
Advanced Planning
Interactive Visualization
Once an initial Master Production Schedule (MPS) has been created, data can be displayed as stock profile graphs and capacity usage graphs. The MPS can be changed by simply clicking and dragging a point on the stock or capacity graphs, and the production of a particular item can be moved from one planning period to another. Any changes made will be reflected in all the linked plot and grid windows.
BOM Level Planning
The planning Bill of Materials (BOM) can be exploded, and then the production plan for lower level items is calculated in the same way. Based on the BOM explosion and the production plan, proposed material purchase requirements can be exported to an ERP system or Excel for action.
Make-To-Stock Planning
Make-To-Order Planning
In a make-to-order environment, stock levels of finished and intermediate items will not be part of the key process parameters. But there will still be the need to evaluate the effects of future demand changes on the manufacturing process. When a change in demand occurs, whether in terms of quantity or delivery dates, there is a need to be able to quickly assess if it is possible to meet the new requirements.
Easily Integrated
No matter your ERP, Opcenter APS easily integrates with its built-in API...
Opcenter Planning Parameters
Planning vs. Scheduling
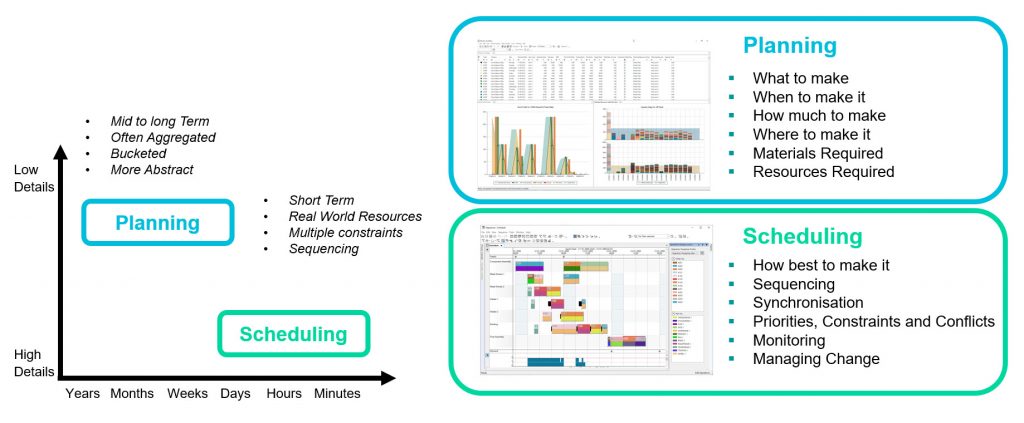